2e main ball mill clinker
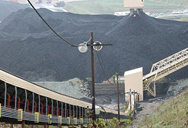
Matrix model of the grinding process of cement clinker in the ball mill ...
2018.2.1 It is shown that the most complete and informative characterization of the grinding process in a ball mill is a grinding matrix taking into account the transformation
More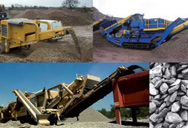
Modeling of closed-circuit ball milling of cement clinker via a
2023.9.1 The aim of this theoretical study is to better understand the complex interplay between ball milling and air classification in full-scale two-compartment ball mills
More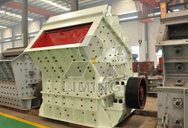
IOP Conference Series: Materials Science and
2023.5.30 The questions of Portland cement clinker grinding in closed circuit ball mills. Noted that the main task of modeling the grinding process is predicting the
More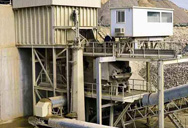
Experimental study of clinker grinding in a ball mill and the
2022.8.18 In this paper, the method was used to study the collisions between grinding media and grinding media and walls in ball mills, which is the most used unit operation in
More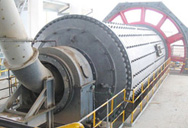
Experimental study of clinker grinding in a ball mill and
2023.6.27 Introduction The cement manufacturing process consists, basically, of the calcination and in the fusion of a material constituted by, approximately, 94% (w/w) of
More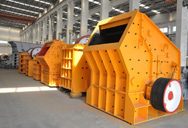
(PDF) Determination of granulometrical composition of the clinker
2020.7.24 PDF This paper presents results regarding the grinding behaviour of two batches of material (clinker) in a ball mill with its own two-step grinding... Find, read and
More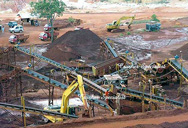
Investigation of flow dynamics of porous clinkers in a ball mill
2019.12.1 Ball mills are usually used for grinding the clinkers to obtain the fine cement powder. A ball mill for clinker grinding usually consists of two chambers
More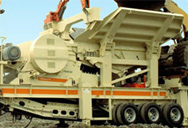
Investigation of flow dynamics of porous clinkers in a ball mill
2019.12.1 1. Introduction Clinker milling is the last step in production of Portland cement. Nodular clinkers produced in a rotary kiln in a cement plant are ground together
More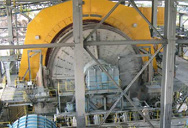
Predictive Controller Design for a Cement Ball Mill
2020.7.26 The schematic diagram of cement ball mill grinding circuit is shown in Figure 2. The clinker, along with additives viz. gypsum, slag, and/fly ash, called feed minerals, are introduced into the horizontally
More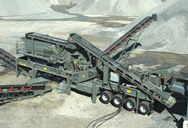
Ball-Mill Grinding Kinetics of Cement Clinker Comminuted in
2015.1.27 Abstract. The use of high-pressure grinding rolls (HPGR) prior to ball mills has become a common practice in cement clinker grinding due to significant energy
More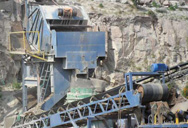
Towards a business case for CO2 mineralisation in the
2022.3.14 Previous work on CO 2 mineralisation has shown that reductions in the range of 0.44 to 1.17 tonne of CO 2e per tonne of CO 2 stored are feasible under today’s energy mix 21 and that the ...
More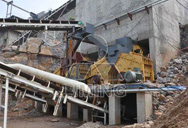
(PDF) CONVENTIONAL CLINKER GRINDING -A NEW
2020.4.29 The L/D ratio of the ball mill was varied in four steps of 1.75, 2.1, 2.79 and 3.49, and the ball charge filling ratio was varied in three steps of 15%, 20% and 25%.
More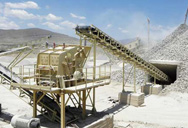
A comparative analysis of steel and alumina balls in fine
2023.3.1 DOI: 10.1016/j.powtec.2023.118454 Corpus ID: 257567488; A comparative analysis of steel and alumina balls in fine milling of cement clinker via PBM and DEM @article{Muanpaopong2023ACA, title={A comparative analysis of steel and alumina balls in fine milling of cement clinker via PBM and DEM}, author={Nontawat Muanpaopong and
More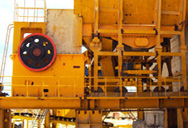
Modeling of closed-circuit ball milling of cement clinker via a
2023.9.1 In the case of a laboratory ball mill for cement clinker milling, the mill dimensions and operation data were taken from [33]. The ball mill's diameter D T was 0.2 m, and the length L T was 0.2 m. Ball filling fraction J T was 0.2, and void filling fraction U T was 0.525. The ball mill rotated at a fractional speed ϕ C,T of 0.75.
More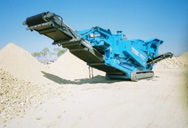
The effect of ball size on breakage rate parameter in a pilot
2009.6.1 Section snippets Experimental studies. Comparative tests were conducted using the different pre-assembled ball charges given in Fig. 1 in a pilot scale ball mill having 1.2. m inside diameter and 0.6 m length.. These six different ball media grading used during the tests runs was identical to industrial standard ball mill media proposed by Bond with
More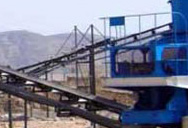
Effects of grinding aids on model parameters of a cement ball mill
2019.2.15 This research focuses on investigating the effects of the three different grinding aids, consisting of a mixture of amine, glycol and polyol in different ratios, on the model parameters of a two-compartment cement ball mill and an air classifier. Within the content of this work, sampling campaigns were organized around a cement grinding
More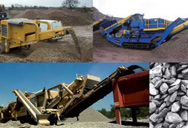
Investigation of flow dynamics of porous clinkers in a ball mill
2019.12.1 The NCCL has three clinker grinding ball mills, all operating in closed circuit configuration. The schematic diagram of the mill investigated and experimental setup is shown in Fig. 1.The mill consists of a cylindrical vessel containing grinding media usually in the form of metallic balls, an elevator and a separator.
More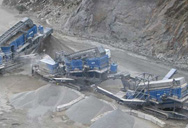
Effects of Mill Speed and Air Classifier Speed on
2021.6.29 Nowadays, ball mills are widely used in cement plants to grind clinker and gypsum to produce cement. The research focuses on the mill speed as well as air classifier speed effect on the two ...
More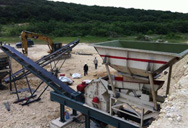
Clinker Production - an overview ScienceDirect Topics
Calcination is the main process of clinker production, calcining calcium carbonate (CaCO 3) at about 900 °C to form calcium oxide, CaO, lime, and the release of carbon dioxide gas (CO 2).In the next step of the so-called clinker treatment, calcium oxide (CaO) is exposed to temperatures of 1400 °C to 1500 °C together with silica (SiO 2), aluminum oxide (Al 2 O
More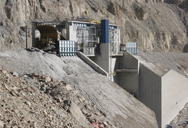
Cement Clinker - an overview ScienceDirect Topics
Application of alkali-activated industrial waste. Jordi Payá, ... María Victoria Borrachero, in New Trends in Eco-efficient and Recycled Concrete, 2019. 13.2.1.5 Industrial wastes. Cement clinker dust (CKD) is a problematic waste derived from the cement industry which may cause some problems in clinkering kiln operations and cement performance. CDW
More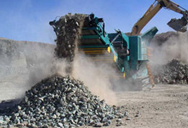
Analysis of material flow and consumption in cement
2016.1.20 Generally, ball mills and vertical roller mills are used. The raw mix is dried by using part of the excess heat from the kiln in the process line or from a stove. The hot air and raw materials are simultaneously fed into the grinding position, dried, and ground. ... Ambient air (2.40 kg/kg cement) and clinker (0.84 kg/kg cement) are the main ...
More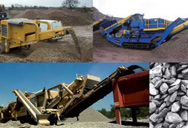
Experimental study of clinker grinding in a ball mill and
2023.6.27 approximately 40% is consumed in the clinker grinding (Jankovic et al. 2004). Despite its energetic eectiveness is very low, ball mills are traditionally the most used devices to the grinding of this material (Camalan and Hoşten 2015; Sridhar, Sankar and Prassad 2016; Mishra et al. 2015). This device consists of a cylindrical drum that horizon-
More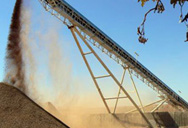
Portland Cement Clinker - an overview ScienceDirect Topics
Portland cement clinker is a hydraulic material which shall consist of at least two-thirds by mass of calcium silicates (3CaO.SiO 2 and 2CaO.SiO 2), the remainder consisting of aluminium and iron containing clinker phases and other compounds.The ratio of CaO to SiO 2 shall not be less than 2.0. The magnesium oxide content (MgO) shall not exceed 5.0%
More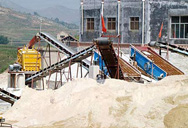
An industrial comparative study of cement clinker grinding
2012.5.1 When only the HPRM system or the ball mill system was operated to produce cements of the same fineness as the combined process cement, the system throughput was reduced to 122.4 t/h in the HPRM-only case and to 72.3 t/h in the ball-mill-only case, with the corresponding specific energy consumptions of 18.8 kWh/t and 35.7
More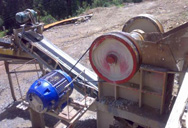
Quantifying the effect of clinker grinding aids under laboratory ...
2015.10.1 Industrial closed-circuit tube (or ball) mill schematically presented in Fig. 1 was used for cement production. The clinker initially passes through a double-deck screen, where all particles larger than 10 mm are sent to a pre-crusher.A measured fresh feed mixture (B0) of pre-crushed clinker, gypsum, and pozzolan is introduced in the mill.
More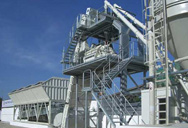
Effects of Mill Speed and Air Classifier Speed on
2020.5.12 Clinker is introduced into the ball mill. The rotating mill is filled with different steel balls of sizes 25 mm, 40mm, 50mm, 60 mm, 70mm and 80 mm with 45%, ... The main separating device is a cylindrical rotor. The rotor is like a cage composed of blades closely spaced. The rotor is operated by a variable speed drive.
More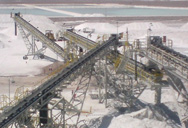
Investigation of flow dynamics of porous clinkers in a ball mill
2019.12.1 Introduction. Clinker milling is the last step in production of Portland cement. Nodular clinkers produced in a rotary kiln in a cement plant are ground together with gypsum into a fine powder of particle size less than 100 μm and with a surface area of 330–380 m 2 /kg for production of ordinary Portland cement (Bye, 1999). The fineness of
More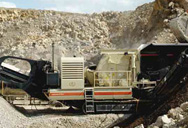
Cement Ball Mill - JXSC Machine
2019.12.10 What is the cement ball mill? The cement ball mill is mainly used for grinding the finished products and raw materials of cement plants, and is also suitable for grinding various ore and other grindable materials in industrial and mining enterprises such as metallurgy, chemical industry, and electric power. Cement grinding is the last process
More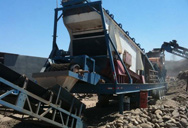
Energy and exergy analyses for a cement ball mill of a new
2020.5.1 The clinker grinding unit mainly consists of a ball mill and a dynamic separator that their technical information is illustrated in Table 1. The initial product is a mixture of clinker, gypsum, and limestone. All components are fed under control from the prebins via a proportioning weigh feeder and a belt conveyor into the ball mill.
More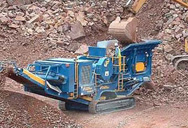
Application of a Method for Measuring the Grindability of
2022.11.15 The VTI method was used as a referral method. The test using the VTI method was conducted in a laboratory ball mill GHOST 15489.1-93 with a porcelain drum with a diameter of 270 mm and a length of 210 mm, see Figure 2. The load consisted of 6 kg of grinding porcelain balls with a diameter of 35 mm and 2 kg of porcelain balls with a
More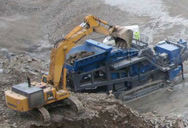
Modeling of closed-circuit ball milling of cement clinker via a
2023.9.1 The aim of this theoretical study is to better understand the complex interplay between ball milling and air classification in full-scale two-compartment ball mills for cement clinker milling. To this end, we modified the true unsteady-state simulator (TUSSIM) for a full-scale open-circuit cement ball mill [4] by coupling the PBM for the mill ...
More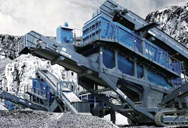
Picture: Loesche GmbH, Germany CEMENT SikaGrind®
2022.7.26 The main disadvantage of Slag Cement is the slow strength development. Slag (ASTM C 989 and EN 15167) or Slag cement (ASTM C 595 and EN 197-1) ... The common intergrinding of limestone and clinker in classical ball mills is therefore producing a cement of very high surface area. The higher the limestone content, the higher the
More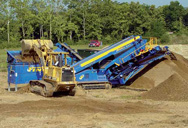
Cement Plant Equipment Technologies for more production
2019.8.8 Clinker Plants: Cement Clinker Grinding Plant is developed with all latest equipment and machines like Pre crusher, feed hopper, Table feeders, Ball mill, Blending, Packing Plant with all Material ...
More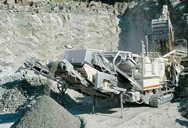
Energy-Efficient Technologies in Cement Grinding IntechOpen
2016.10.5 The energy consumption of the total grinding plant can be reduced by 20–30 % for cement clinker and 30–40 % for other raw materials. The overall grinding circuit efficiency and stability are improved. The maintenance cost of the ball mill is reduced as the lifetime of grinding media and partition grates is extended. 2.5.
More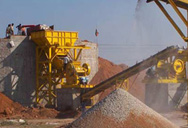
Predictive Controller Design for a Cement Ball Mill Grinding
Chemical process industries are running under severe constraints, and it is essential to maintain the end-product quality under disturbances. Maintaining the product quality in the cement grinding process in the presence of clinker heterogeneity is a challenging task. The model predictive controller (MPC) poses a viable solution to handle the variability. This
More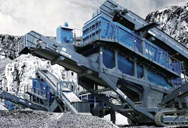
Construction Materials with Low Power Intensity Based on
2021.3.29 1 Introduction. Cement production is associated with high energy costs, which amount to about 110 kWh/t of cement, while from 40 to 50% (depending on the method and culture of production) falls on the cement grinding shop, i.e. on average 40 ± 5 kWh/t is spent on clinker grinding [ 1, 2 ]. These figures show the need to improve the
More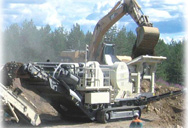
(PDF) IMPROVING PRODUCTIVITY BASED ON THE
2019.12.25 As a result, a change in the behaviour of clinker movement would occur inside the cement mill, that is, the fineness clinker penetrates the grinding balls, and thus reducing the grinding ...
More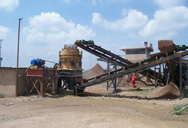
(PDF) Determination of granulometrical composition of the clinker
2020.7.24 The energy consumption of grinding is the subject of many studies, especially in the case of ball mills for grinding clinkers [8, 9], fuels [10], iron ore [11], hematite ore [12], sulfide ore [13 ...
MoreArticle aléatoire
- la machine concasseur deuxième prix de la main
- minoteries humide du maïs dans
- equipamentos auxiliares na minerao
- Machine Indonésie Rectifier Le Quartz De Silice
- sandbag machine de remplissage
- combien coûte un concasseur à mâchoires série pe
- commerciale moulin à épices melbourne
- concasseur de pierre roger
- concasseur plante royaume uni
- charbon et des cendres systeme de manutention ppt
- pour broyeur de pierres dans luttar pradesh suppliersmall
- équipement pour couper le granit
- occasion de concassage de pierre Indonésie vendre
- machine à prix diamant de pierre à dubaï
- densité en vrac pour concasseur run
- raymond fabricant de moulin en nous
- maison de pulvérisateur pour charbon
- broyeur de pierre minerai de fer
- entrepreneurs charbon balikpapan minière
- theorie broyeur à boulets
- fournisseurs de concasseurs de bentonite
- broyeur de pierres méthode de projet détaillé bangalore
- prix de 4 broyeur en pierre ollaire de broyage
- diagramme de flux du processus de minerai d hematite
- route en béton de concasseur
- machine pour broyer le sumac
- machines et outils de sable pvt ltd
- agregees fabricants de concasseurs fournisseurs en Inde une
- ventes granit de concassage de Belgiqueia
- concasseur pierre de cône entreprises
- avantages et les inconvénients de concasseur à machoires concasseur giratoire à
- concasseur à cône indiadirectory concasseur machines
- charbon moulin problème de démarrage
- liste de la plante concasseur à haryana
- equipement de securite de la machine concasseur
- concassage et criblage dusines en calcaire